Case Study: Enhancing leakage management and operational efficiency with FYLD
The challenge
The client, a prominent provider of water and wastewater services, faced significant challenges in managing leaks and ensuring operational efficiency. The existing processes were cumbersome, leading to inefficiencies and increased costs.
Key challenges included:
- Prolonged leak durations causing water loss and financial penalties.
- Ensuring field worker safety while complying with regulations.
- Difficulty in real-time monitoring and managing field operations.
- Inefficient resource allocation, leading to redundancies and wasted efforts.
The trial aimed to address these challenges by providing a scalable solution that could enhance productivity, reduce costs, and improve safety outcomes.
The solution
FYLD implemented a comprehensive, AI-powered solution tailored to the client’s needs during the 12-week pilot. The key components of the solution included:
- Redesigned 591 leakage jobs with FYLD’s AI-driven approach. The pre-trial average time for leak resolution was 5 days, which was reduced by 1.4 days during the trial. This improvement resulted in saving 2 megalitres of water per day.
- Conducted over 2,223 video risk assessments, significantly improving hazard identification and safety compliance.
- Provided a real-time view of job progression, enabling better remote management and proactive interventions.
- Ensured seamless coordination between teams, reducing the need for repeat visits and minimising non-value-adding tasks.
Additionally, the solution facilitated:
- Enhanced data collection, improving decision-making and responsiveness.
- A shift from reactive to proactive safety measures, reducing incidents and promoting safer work practices.
- Optimised resource utilisation, eliminating non-value adding work and improving operational efficiency
By deploying FYLD’s technology, the client was able to streamline operations, enhance safety protocols, and ensure better compliance with regulatory requirements.
Process improvement for leakage reduction
Through FYLD’s innovative process redesign, the entire leakage management workflow—from detection to repair—was transformed. The implementation of real-time video documentation during leak detection, combined with virtual planning reviews and continuous job progress monitoring, eliminated inefficiencies such as unnecessary site visits and communication delays.
This redesign not only reduced leak run times and rework but also enhanced the quality of repairs and optimised resource allocation, ensuring swift and effective leakage management.
Conclusion
The partnership between the client and FYLD proved highly effective in addressing key operational challenges. The successful pilot highlights FYLD’s potential to transform operational workflows, enhance safety protocols, and deliver significant cost savings. The client is now well-positioned to continue leveraging FYLD’s technology for ongoing improvements in their water management processes.
This case study underscores FYLD’s commitment to driving value through innovative solutions, ultimately supporting the client’s mission to provide efficient and safe water services.
Proven impacts
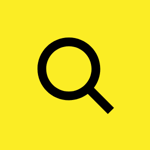
Cost savings
- Estimated total savings of £1.35 million.
- £351k in leakage savings and £62k in time savings from reduced RFAs.
- Significant reduction in costs driven by FYLD implementation, resulting in an approximately 80% cost reduction for applicable leakage volumes compared to the estimated cost of £1 – £1.2 million per megaliter reduction using traditional methods.
Operational efficiency
- Achieved a 20% reduction in job blockers.
- Reduced leak run time by 35% in trial areas, saving an average of 1.4 days per leak.
- Achieved a 15% reduction in re-work, significantly minimising the need for additional labour and resources.
Safety enhancements
- Conducted 2,223 dynamic video risk assessments.
- Increased remote manager interactions to 12%, enhancing oversight.
- Improved hazard spotting and incident reduction, fostering a safer work environment.
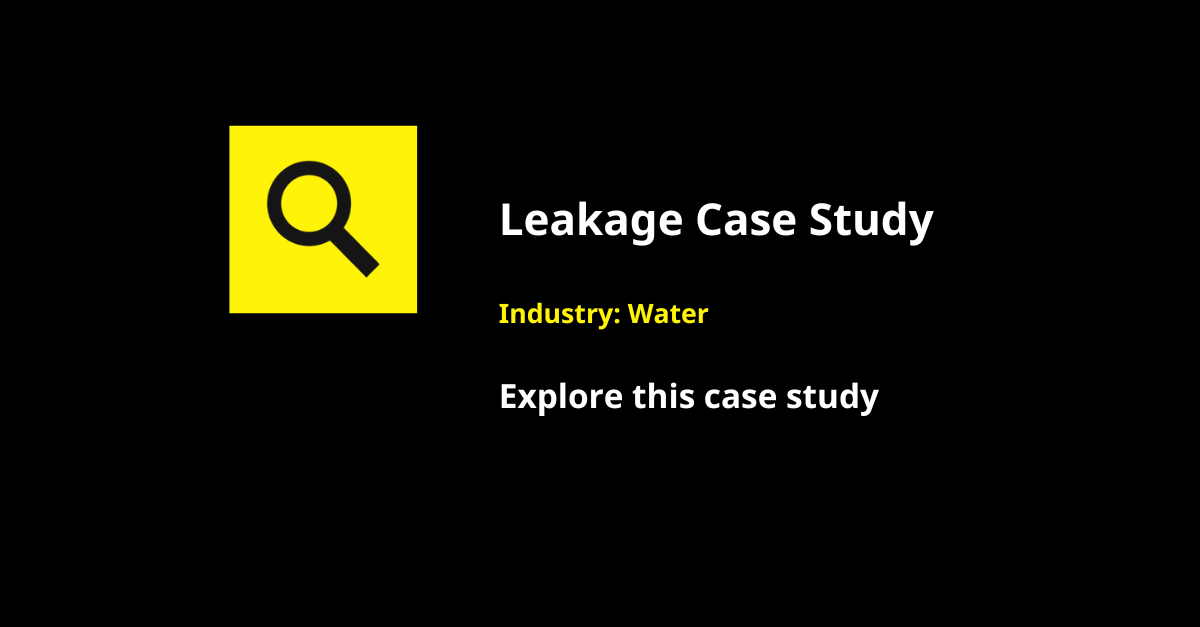